Selection of Steam Traps F&B Devices
Devices: Kneaders, Kettles
[Explanation] Manufacturing in the F&B industry involves steaming, boiling, mixing, and other such processes. There are many devices that use steam in these processes, with examples of such devices including
kneaders and kettle mixers (jacketed kettles).
As these devices are normally used for batch production, air enters the mixer when an operation finishes, and it must be reliably discharged in order to ensure optimal performance during operation.
This means that the devices must have an air vent.
[Choosing Traps] Mechanical (bucket/float) or diaphragm traps should be selected if condensate is to be recovered, or thermodynamic disc traps can also be considered for selection if it is not.
Remember that models with a bypass/blowdown valve function greatly reduce pipework and installation costs.
Kneaders
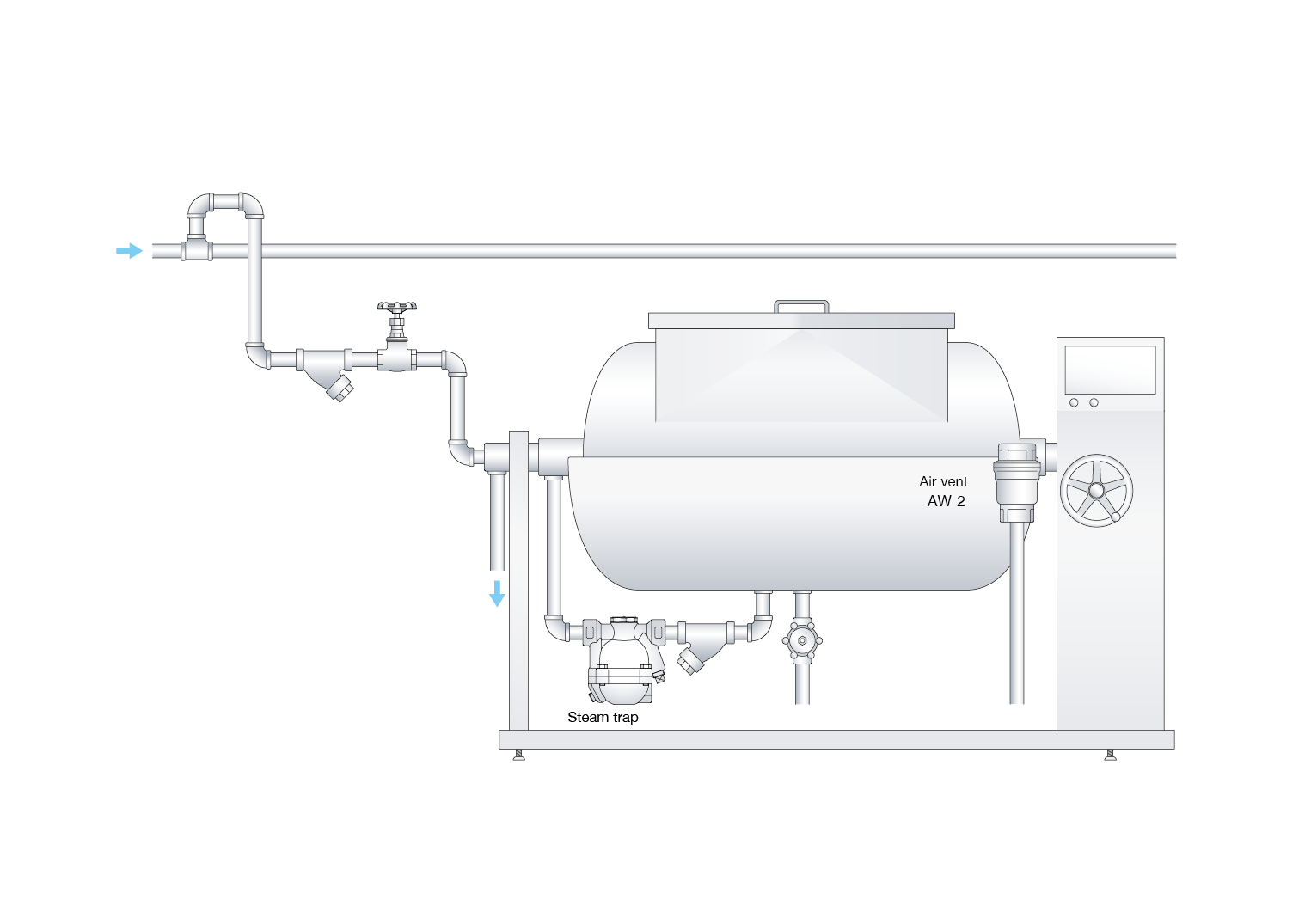
Steam enters the mixer via the strainer, pressure gauge, and pipes at the bottom of the mixer.
Condensate flows out from the bottom of the mixer and into a trap.
If air cannot escape from the mixer then a short circuit occurs and the steam that is supposed to fill the mixer flows into the trap, and it is not heated sufficiently.
Therefore, an air vent must be included to ensure the device can perform to its full capacity.
Total capacity of heated object (ℓ) | 100-1000 | |||
Approximate steam usage rate (kg/h) | 50-170 | |||
Model | Float Trap G20N-8 ![]() |
Diaphragm Trap (with bypass/blowdown valve function) DV1-10H ![]() |
Disc Trap (with bypass/blowdown valve function) SV-N-2 ![]() |
|
Installation | Horizontal pipe | 〇 | 〇 | 〇 |
Vertical pipe | — | 〇 | 〇 | |
Operating features | Continuous operation | 〇 | 〇 | — |
Intermittent operation | — | — | 〇 | |
Features | Energy saving | ☆☆☆ | ☆☆☆ | ☆ |
Condensate recovery | ☆☆☆ | ☆☆☆ | ☆ | |
Initial cost | ☆ | ☆☆☆ | ☆☆☆ |
Kettle Mixers (Jacketed Kettles)
In the examples below, the condensate discharge outlet is at the bottom of the mixer.
Fixed Type
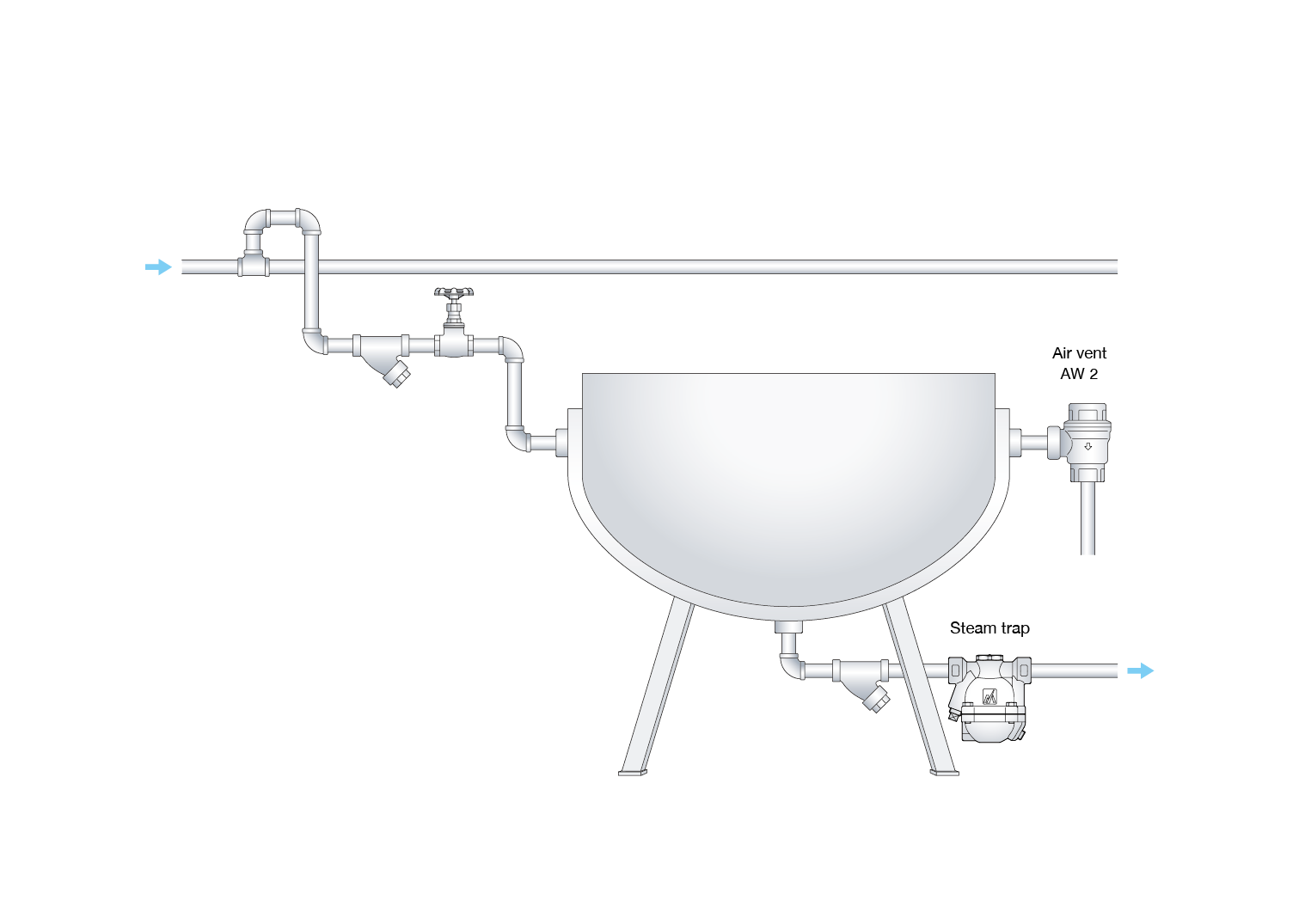
Rotating Type
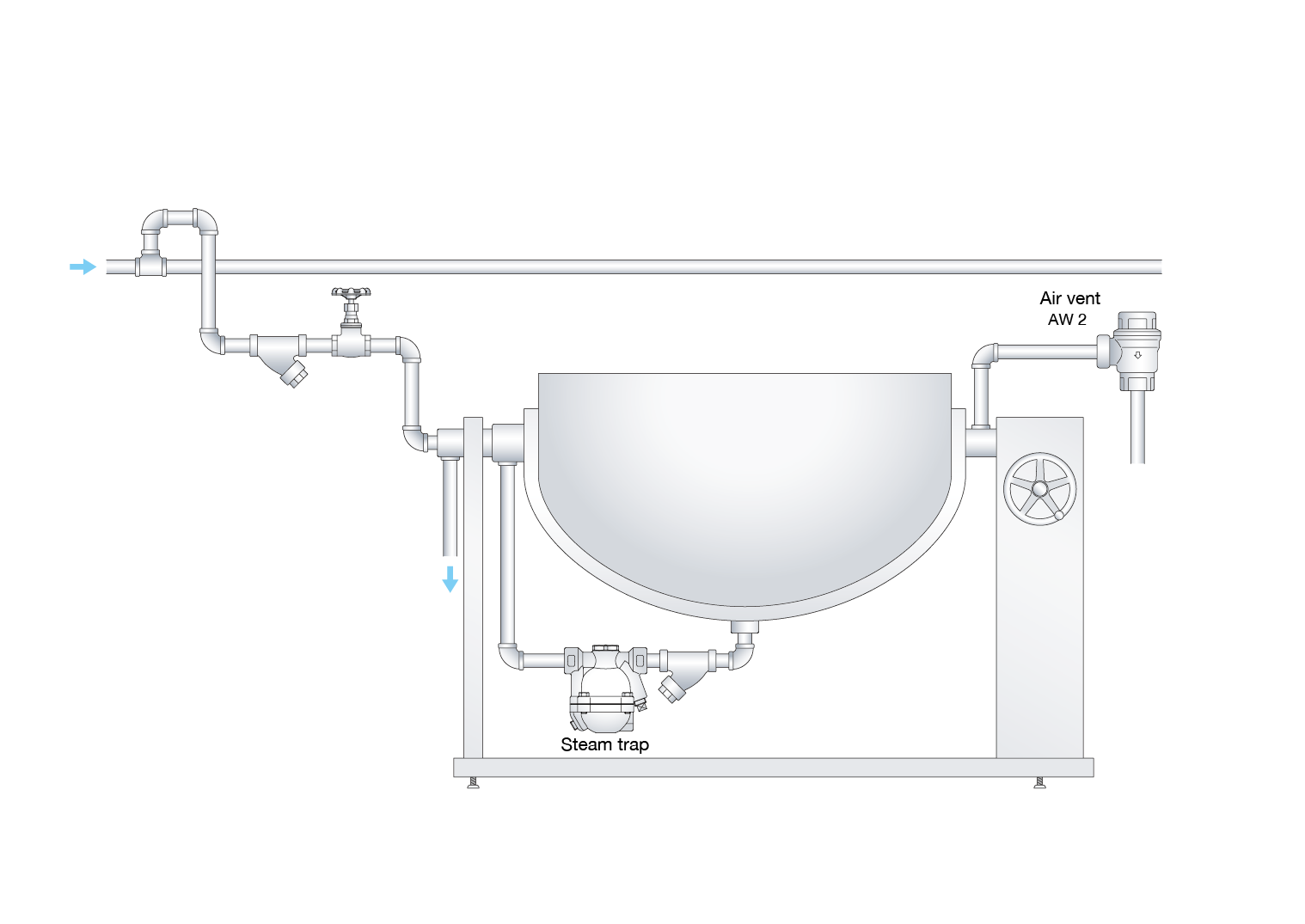
Steam enters from the side of the mixer, and it becomes condensate after heating the mixer. The condensate then escapes to the trap from the bottom of the mixer.
In order to ensure even heating in a kettle mixer, an air vent must be included to swiftly expel the air when steam initially starts to flow.
Total capacity of heated object (ℓ) | 100-1000 | |||
Approximate steam usage rate (kg/h) | 50-200 | |||
Model | Float Trap G20N-8 ![]() |
Diaphragm Trap (with bypass/blowdown valve function) DV1-10H ![]() |
Disc Trap (with bypass/blowdown valve function) SV-N-2 ![]() |
|
Installation | Horizontal pipe | 〇 | 〇 | 〇 |
Vertical pipe | — | 〇 | 〇 | |
Operating features | Continuous operation | 〇 | 〇 | — |
Intermittent operation | — | — | 〇 | |
Features | Energy saving | ☆☆☆ | ☆☆☆ | ☆ |
Condensate recovery | ☆☆☆ | ☆☆☆ | ☆ | |
Initial cost | ☆ | ☆☆☆ | ☆☆☆ |
Kettle Mixers (Jacketed Kettles) with Siphon
In the below example, condensate is discharged from the side rather than the bottom of the mixer.
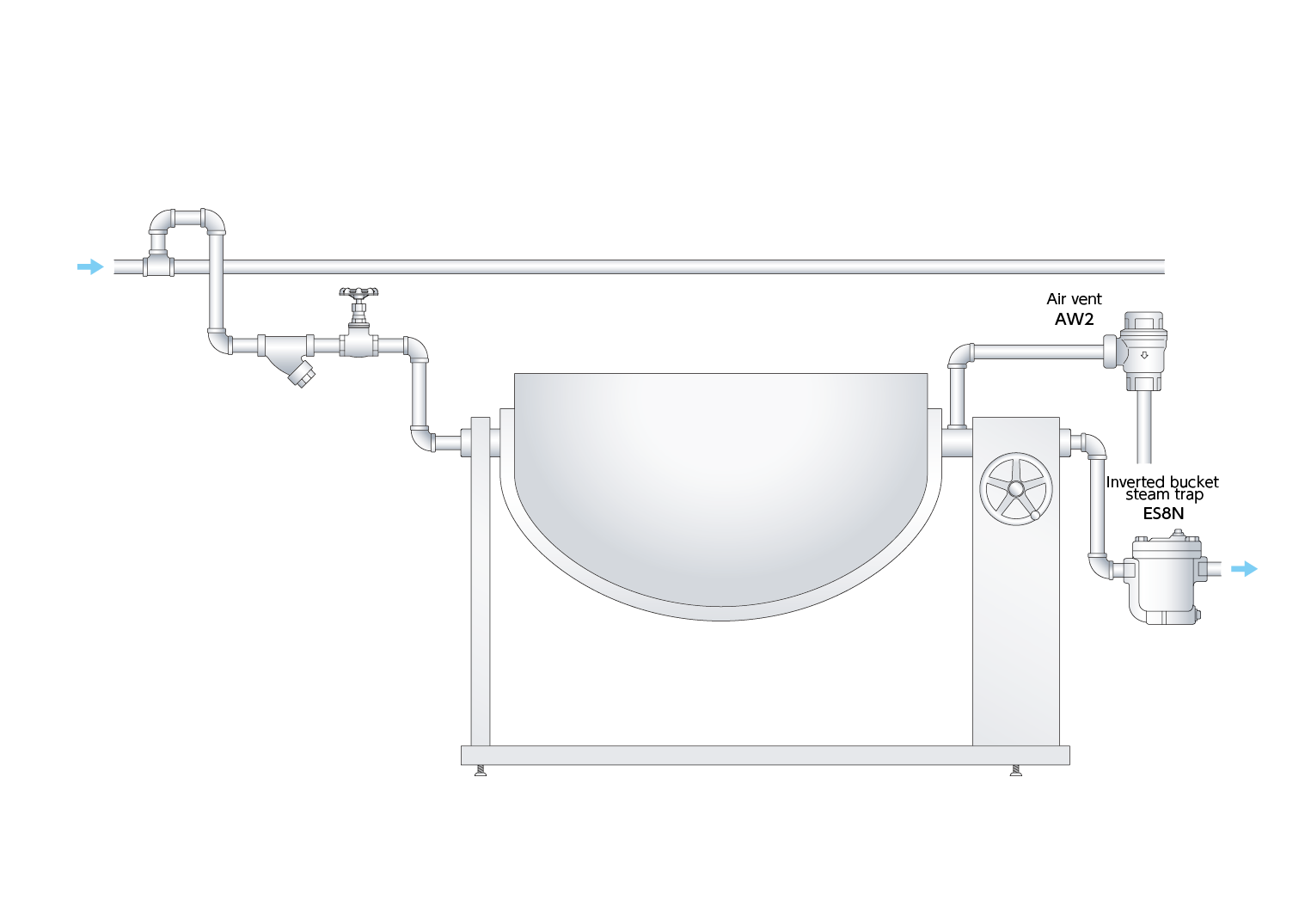
Some rotating kettle mixers use a siphon pipe.
Steam enters from the side of the mixer, and it becomes condensate after heating the mixer. The condensate then accumulates at the bottom of the mixer and is drawn to the trap via a siphon pipe.
Steam locking temporarily occurs in devices that use siphon pipes, so this means bucket-type traps that have an air vent hole (orifice) are more suitable than float-type traps in which the air vent opens and closes according to temperature.
For devices like these, the highest priority is given to the selection of locking measures.
Total capacity of heated object (ℓ) | 100-1000 | |||
Approximate steam usage rate (kg/h) | 50-200 | |||
Model | Bucket Trap ES5-7 ![]() |
Bucket Trap ES8N-8 ![]() |
Disc Trap (with bypass/blowdown valve function) SV-N-2 ![]() |
|
Installation | Horizontal pipe | 〇 | 〇 | 〇 |
Vertical pipe | — | — | 〇 | |
Operating features | Continuous operation | — | — | — |
Intermittent operation | 〇 | 〇 | 〇 | |
Features | Energy saving | ☆☆☆ | ☆☆☆ | ☆ |
Condensate recovery | ☆☆☆ | ☆☆☆ | ☆ | |
Initial cost | ☆☆ | ☆☆ | ☆☆☆ |
[Air Vents] An air vent is a device to shorten the start-up time of steam piping and equipment.
This enables the swift discharge of air, an incompressible gas, from within the device and a reduction in the time for it to fully function.
The compact AW2 is recommended for kneaders and kettle mixers.
The AT9N is recommended for steam ducts.
Please feel free to speak to us if you require the body to be made of stainless steel.
Total capacity of heated object (ℓ) | 100-1000 | ||
Approximate steam usage rate (kg/h) | 50-170 | ||
Model | Air Vent AW2 ![]() |
Air Vent AT9N ![]() |
|
Installation | Horizontal pipe | 〇 | |
Vertical pipe | 〇 | ||
Angled pipe orientation | 〇 | ||
Specifications | Max. usage pressure | 0.5MPa (72.5psig) | 1.6MPa (232psig) |
Max. usage temperature | 150℃ (302℉) | 350℃ (662℉) | |
Body material | Brass (C3771) | Carbon steel (A105) |